Art./Item | ![]() | ![]() | ![]() |
---|---|---|---|
10820 | 35 | 400 | ![]() |
10821 | 35 | 400 | ![]() |
22110 | 35 | - | M/Ricambio legno |
Hammer for bricklayer with forged steel head with chisel swing and one with elongated point functional for demolition work.
Kapriol hammers are available with two different versions of handle: one in three-component plastic with high grip that guarantees a firm grip, the other in certified beech wood and painted, both with conical anti-slip groove.
TECHNICAL SPECIFICATIONS
- head painted with epoxy powder
- Chisel and one very long tip
- version with plastic handle Progip Tri-component with fiberglass core
- version with handle in certified beech wood painted
- handles made with conical countersunk anti-slip
MATERIALS
- Head: hardened forged steel
- Handle: beech wood or three-component plastic
Materials
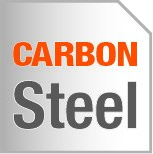
Carbon Steel
Designed to guarantee high striking yield
Tri-component grip
Production technologies
Kapriol blacksmith mallets are designed to guarantee professional users get the best striking yield. Balanced weight distribution makes them well-balanced and especially comfortable to use due to the ergonomic handles.
Research on head shape and weight guarantee high strike yield. Striker surfaces are subject to accurate mechanical grinding processes to make them flat and efficient when used. Specific heat treatments guarantee excellent impact wear resistance.
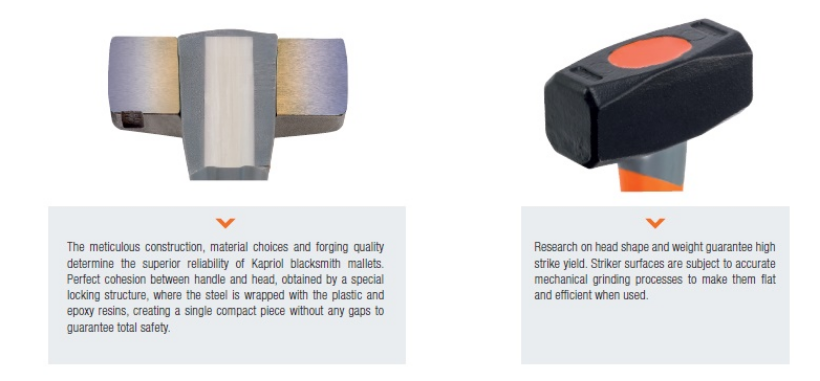
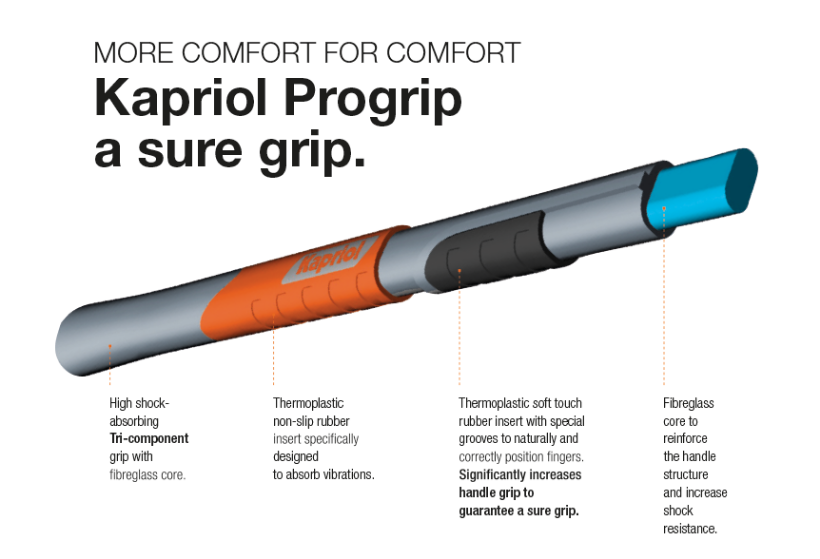
Kapriol blacksmith mallet production technologies - Hot-forged
Although is the oldest form of metalworking, forging is the best blacksmith mallet construction technology. This production procedure occurs using closed moulds that ensure that the part has a defined shape, very close to the end article, at the end of the process.
The production cycle includes all those operations that start with preparing and cutting the piece of material: the billet, semi-processed top-quality and certified steel, obtained through casting or lamination processes, that is heated to a temperature of 850° C thanks to the powerful induction furnaces. The heated part is then placed in the moulds which, driven by presses with variable power from 450 to 650 tonnes, grants the required shape.
The press-forge process, compared to other processes, provides the product with higher mechanical resistance due to the fibre layout and material compaction that occurs in the compression phase.
The press-forging process also guarantees the elimination of most of the potential internal raw material defects due to high compression obtained during the mould closing phase.
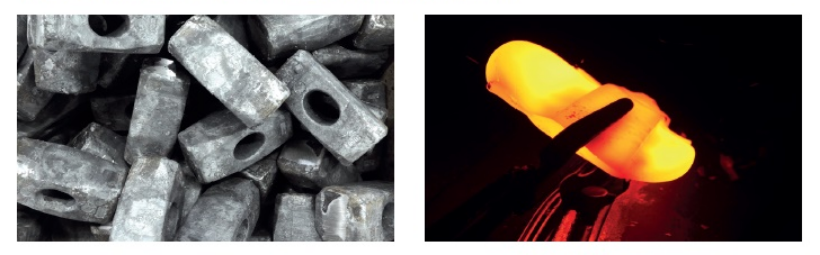